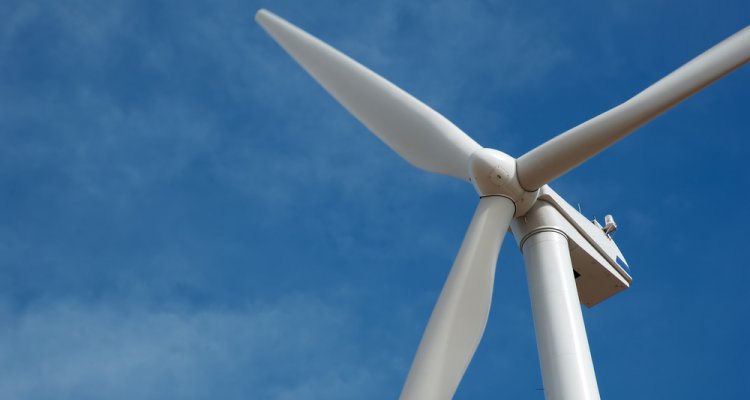
News
ESTELLA project: developing a new generation of recyclable bio-composites
They can be produced in any shape, but after curing they are strong, light, UV- and heat-resistant and resistant to aggressive chemicals. This makes thermoset epoxy composites ideal for demanding applications, for example in aircraft, cars, wind turbines or construction. However, the impressive performance of these special materials also makes them resistant to recycling. Moreover, they are often composed of fossil and toxic raw materials. The European ESTELLA project is changing this.
The ESTELLA is a research project funded by the European Union’s Horizon Europe research and innovation programme and co-funded by WUR’s Knowledge Base Programme KB-34 “Circular & Climate Neutral Society” (KB-34-003-009) , supported by the Dutch Ministry of Agriculture, Fisheries, Food Security and Nature. Within ESTELLA, 13 research institutions and companies from 8 European countries [see box 1] are working together to develop epoxy thermosets and their bio-composites [see box 2] that are circular and safe, and preferably also biobased and biodegradable: the so-called Safe-and-Sustainable-by-Design approach.
The microstructure of these materials does not make that easy, explains Ghazal Tavakoli Gheinani. She is project leader and researcher at Wageningen University & Research (WUR). “Traditional thermoplastics consist of more or less parallel, long polymer chains, which can slide pass one another when heated. This allows us to melt, reshape and recycle them. Thermosets also consist of polymer chains, but they are cross-linked. These extra bonds fix the position of the polymer chains in relation to each other. So if you heat them, or if you apply some other kind of stimulus, the structure of the material remains stable. It means you can't melt it, you can't reshape it, you can't recycle it, nothing.”
Covalent Adaptable networks
Wageningen Food and Biobased Research (WFBR) as one of the partners of the ESTELLA project is looking for ways to re-design the cross-linked structure of thermosets, by introducing Covalent Adaptable Networks (CAN). Unlike the traditional thermosets, the bonds in CAN-containing thermosets are semi-permanent. Under normal conditions and in the absence of stimuli, these materials are stable and behave as a traditional thermoset. However, they can be altered by applying specific stimuli, for example heat, UV light or chemicals with a certain acidity. Tavakoli: “In our project, for example, we are applying the so-called Diels-Alder chemistry. Diels-Alder bonds can be reversed upon response to, e.g. elevated temperatures as stimulus. Once the cross-links are broken, the material behaves like a thermoplastic and you can recycle it the same way.”
It is also worth mentioning that, compared to other current recycling methods such as pyrolysis or solvolysis, this approach requires much less energy and eliminates the use of harmful chemical solvents. Furthermore, in all previous recycling techniques, the emphasis has primarily been on recovering the fibres rather than the polymer matrix, as fibres represent the more costly component of composites. “This focus has led to these methods being classified as down-cycling. In contrast, our approach holds the potential for efficient and effective separation and reuse of both fibres and resins, thereby enabling a more sustainable recycling process.”
In this way, the ESTELLA project is working with diverse consortium partners to design and develop a new generation of composites that are biobased, circular and environmentally friendly, as well as economically viable. The new materials are being tested in two concrete applications: a scooter platform and a window frame. These products have been selected from sectors where mechanical performance is critical, in this case mobility and leisure, and construction. If the prototypes are successful, the formulations could also be used in other applications, which require similar mechanical and thermal properties.
Test pieces
Meanwhile, the ESTELLA project has been underway for more than two years. No full prototypes have been produced yet, but some test pieces have. “We still have a year to go,” says Tavakoli. “Hopefully by the end of this year, we will have some promising formulations that meet the ESTELLA requirements, and then we can start focusing on application and scale-up. In any case, we are already thinking about a follow-up project.”
Commercial availability of the new materials, however, Tavakoli says, will at least take another five to ten years . Interest from industry is already there. “After all, there is no alternative to thermoset composites yet. And because they are not recyclable, the European regulations are putting a lot of pressure on various industries to find sustainable and less environmentally damaging options for these materials. Therefore, I certainly expect that funds will be released for follow-up research.”
The ESTELLA is a research project funded by the European Union’s Horizon Europe research and innovation programme and co-funded by WUR’s Knowledge Base Programme KB-34 “Circular & Climate Neutral Society” (KB-34-003-009) , supported by the Dutch Ministry of Agriculture, Fisheries, Food Security and Nature.