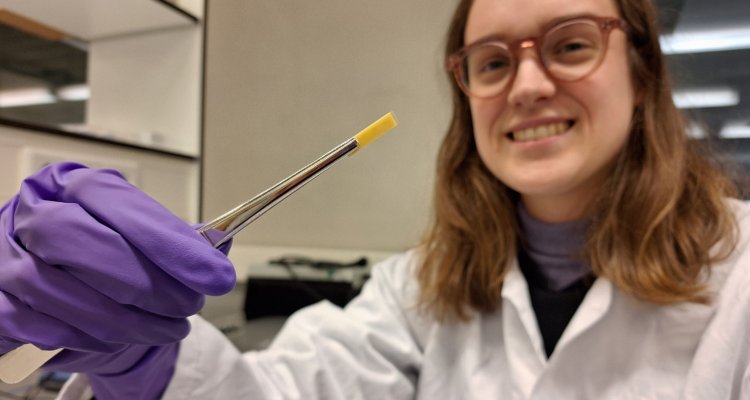
News
Creating a new, sustainable plastic using physics
For the past three years, PhD candidate Sophie van Lange has been dedicated to one clear goal: producing plastic that is both hard and sustainable. The plastics we use today are either recyclable or strong and hard – not both. Van Lange stepped away from traditional chemical approaches to produce plastic and developed a completely new method to create durable and reusable plastic in a completely new way. The trick? Physical forces.
The process begins with a seemingly simple setup: a yellow powder in one dish and a white powder in another. By dissolving and combining these two solutions, and subjecting them to heat and pressure in a hot press, Van Lange transforms these substances into a rectangular piece of plastic measuring two by half a centimetre within two weeks. Under normal conditions, the resulting plastic is sturdy and hard but becomes reformable when heated. She refers to these innovative plastics as "compleximers”. Van Lange and her colleagues report on this in the scientific journal Science Advances.
Sustainable Plastic Processing
Plastics are ubiquitous in our daily lives, serving as packaging for peppers and cucumbers in the supermarket, or as packaging of new toys. “But plastic is also incorporated in the shoes on my feet and the glasses on my nose,” says Van Lange, pointing to her pink frames. Yet we rarely think about what happens to these materials after the shoes break or when you need new glasses.
How great would it be if we could process all plastics sustainably?
"You can take old items to a recycling point, but hardly anyone knows exactly what happens to them afterward," says the young researcher. Consider a shoe sole, which is also a type of plastic. After use, we cannot do anything with it, except burn or grind it. Other plastics, like the bag around a pepper or the layer in a milk carton, can be recycled. "How great would it be if we could process all plastics sustainably," Van Lange wonders aloud. She is driven by her love for sustainable materials and works on this innovative plastic in the Physical Chemistry and Soft Matter chair group. “I think sustainable materials are really cool,” she says, beaming.
"On a molecular scale, plastics consist of long chains," explains Van Lange. In traditional hard plastics, these chains are connected by chemical cross-links for strength. However, these cross-links are so robust that recycling becomes nearly impossible. That is why Van Lange redesigned these plastics without chemical cross-links, this time utilizing adjustable physical forces.
Force of attraction
"Half of the chains that make up our plastic are positively charged," Van Lange explains. "The other half is negatively charged." When you bring them into contact with each other in the right way, they attract each other, just like two magnets. This keeps the chains together without the need for chemical cross-links. When heated, the attraction between the parts weakens, allowing the entire material to reshape. "This enables the plastic to be reused or, for example, to repair a hole or other damage in the plastic with heat," says Van Lange.
The innovation lies in sufficiently weakening the charge
So far, the PhD candidate has produced approximately three grams of the new plastic. "It took a while before my colleagues and I actually had the desired plastic," she says. It all boiled down to attraction: in nature, positive and negative particles strongly attract each other. This makes materials brittle and nearly impossible to deform when heated. "The innovation lies in sufficiently weakening that charge," says Van Lange.
She achieved that with a kind of “molecular umbrellas” that partially shield the positive and negative charges in the plastic. "That is how we achieved the perfect attraction force and, consequently, plastic that is easily deformable when heated," says the PhD candidate. Moreover, these umbrellas are water-repellent, ensuring the plastic remains robust when exposed to water. That was, a shoe sole made from the new plastic stays sturdy when stepping into a puddle. "Charged material is almost always sensitive to water, so achieving this is very special," adds Van Lange.
I want to motivate other scientists to look at materials differently and use them in unconventional ways
More flexibility
The new plastic is not yet entirely ready yet. For example, the material is not yet flexible enough, according to Van Lange: "We demonstrate that the concept works, but now we need to find a way to give it more rubber-like properties." The researcher hopes to achieve this by reducing the charge in compleximers, perhaps by adjusting the building blocks of the chains that make up the plastic. "An alternative could be to enlarge the molecular 'umbrellas,'" says Van Lange. She also considers altering the type of chains. "We currently use polystyrene, a stiff molecule," explains the PhD candidate. "If we replace it with a more flexible variant, we might already get a more bendable plastic."
Although the plastic is not yet ready for the market, the PhD candidate hopes that her work will inspire other researchers. Her research demonstrates that thinking outside the box can lead to entirely new materials. "I want to motivate other scientists to look at materials differently and use them in unconventional ways," concludes Van Lange.