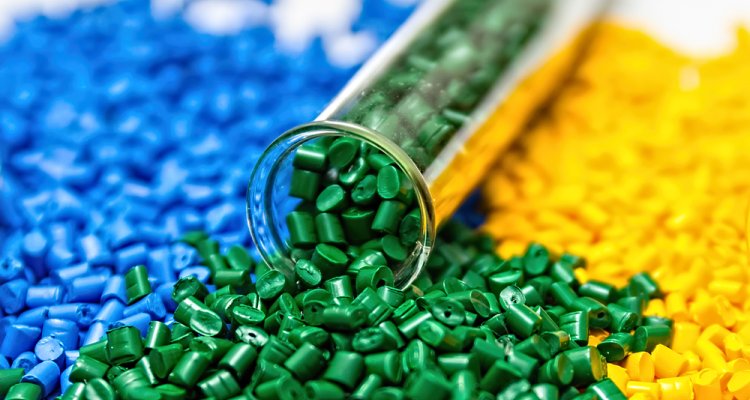
Connecting story
Hard plastics can be recycled if they are constructed differently
Rigid plastic is very useful but is difficult to recycle. At least, that was the case until the discovery of so-called vitrimers. Researchers of the Biomolecular Sciences cluster have laid the foundation for this new type of sustainable plastic, which is hard when possible and soft when needed.
The first plastic made entirely of petroleum was invented over a century ago. Chemists soon discovered that small alterations in the building blocks of plastics could change the properties and thus create new types of plastic. Since then, this strong, cheap material has become indispensable in our society. We have plastic window frames and other building materials, plastic cups and bottles, tyres and dashboards, lenses, laptops and toys. Not to mention, the majority of our food is wrapped in plastic.
Still, the increasing pollution caused by plastic in nature is an obvious downside. The percentage of plastic waste that is recycled globally oscillates around a few per cent. The remainder is incinerated, dumped or disappears into the environment. Hence, chemists are searching for methods to make infinitely renewable plastic with convenient properties. That is quite a challenge. Recyclable plastic already exists, but this plastic is rather soft and thus less suitable for the manufacturing of car parts or rigid packaging.
A new invention
In existing hard plastics, the smallest building blocks, the molecules, consist of long strands, as is the case in all sorts of plastic. However, in hard plastics, these strands are interlinked with strong connecting links. These links remain in place even under high temperatures. This makes it difficult to recycle hard plastic because once formed, it cannot be transformed. Five years ago, Wageningen chemists decided to continue working on vitrimers, a French invention that combines the advantages of hard and soft plastics.
At the Organic Chemistry group, Simon van Hurne, Sybren Schoustra and their supervisor Maarten Smulders work on this new sustainable plastic. ‘You may see a vitrimer as the net in a soccer goal that has been knotted together’, says Schoustra. ‘That network can be activated, which unties the knots and enables you to re-tie them elsewhere.’ The vitrimer is activated through heat. ‘Preferably, you would have something that is hard at room temperature and becomes malleable at 150 degrees Celsius. Because you don’t want your mug to collapse as soon as you pour hot coffee in it’, says Schoustra.
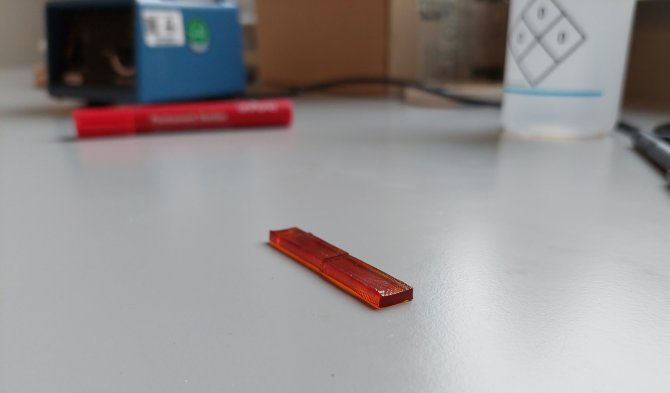
Testing with others
Schoustra and Van Hurne take their new pieces of plastic to other researchers to test the properties. One of these locations is their neighbour, the laboratory of Physical Chemistry and Soft Matter. Here, they placed pieces of plastic in a rheometer to test how rigid or elastic the material is and until what temperature it remains stable. Jasper van der Gucht, who works in the lab, explains: ‘Our rheometer pushes and pulls the material to see how strong it is. Simon and Sybren come to us for these measurements, and we help them interpret the data. We complement each other.’
Schoustra then moves one door further down to the Biophysics group. ‘This collaboration started as a Friday-afternoon experiment’, Schoustra says. ‘But, we instantly saw interesting things. Now, we have been collaborating for one-and-a-half years.’ He uses this group’s Raman microscope to study the minute details of new materials. He investigates the precise composition of the material and how its molecules are arranged. ‘If everything is properly arranged at a molecular level, you should be able to see right through the plastic. That is important for some applications; people like to be able to see what they are buying.’
Soluble in seawater
There is hope that products made from this new plastic will be recycled and don’t end up in the environment. Should this happen anyway, a new type of biobased plastic developed by Julian Engelhardt may offer a solution in the future. Engelhardt works for Wageningen Food and Biobased Research and the Organic Chemistry and Soft Matter group. The plastics he tries to develop are called saloplastics. This material disintegrates into harmless molecules in salt water. ‘It can be broken down in a few days, weeks or months’, says Engelhardt. In contrast, other plastics can float around in the ocean for dozens, or even hundreds, of years,
The principle works, but Engelhardt is still tweaking the material to make it strong enough for application in products. The fact that his project is a collaborative effort between two groups and a research institute is a major advantage. ‘I have easy access to equipment in three different locations. This shared position also means I have an extensive network of researchers at my disposal, which accelerates my project.’
Van Hurne also feels that the shared equipment and easy access to other researchers are key benefits of this collaboration. ‘Working together means you can just walk in, and it also helps you get new ideas for your next research project.’
The work of Schoustra and Van Hurne was supported by a Vidi grant (to Maarten Smulders), awarded by the Dutch Research Council (NWO).