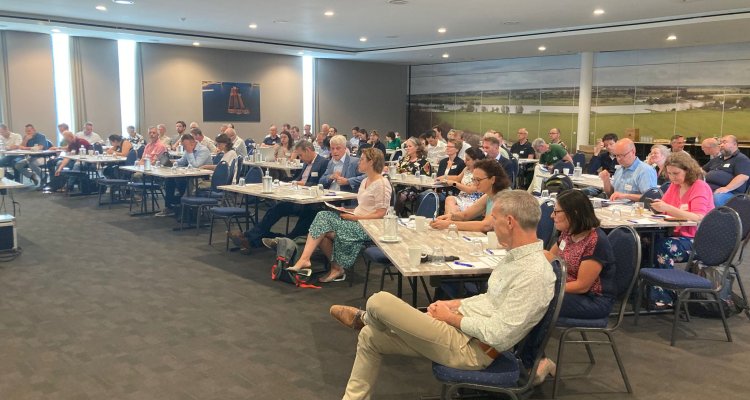
Looking back
Cooperation helps industry sustainability take a step forward
Biobased materials need not be inferior to those from the traditional fossil-based industries. Wageningen Food & Biobased Research has been demonstrating this for years within her research programmes, in which Wageningen University & Research (WUR) researchers work with companies on greening industrial production. This was again evident on June 22nd 2023 at the annual Circular and Biobased Products Symposium, the 10th in the series.
Cooperation with industry is not a given, microbiologist and writer/columnist Rosanne Hertzberger noted. Hertzberger acted as the symposium's chair for the day and immediately set the cat among the pigeons. When it comes to confidence among the general public, science is somewhere near the top, while industry tags along near the bottom. This is partly because of 'industrial storytelling': the magnificent stories companies tell about the sustainability of their products or processes, for example about 'flying responsibly' on biokerosene, or about how clean diesel cars are. Assisted by government funding, they are investing large sums of money in small intermediate steps towards climate targets. Time and money are wasted in this way on solutions that are no solutions at all in Hertzberger’s view: storing CO2 underground or under the sea, pyrolysis of biomass and waste plastics to make ‘bio-naphtha' for the crackers of the chemicals giants, adding biomass to the fuel for power stations and using agricultural land for fuel or fodder, instead of food crops. Greenwashing, in Hertzberger’s opinion. And that is the same as storytelling. Academics are colluding with this, she believes. Energy-intensive traditional chemistry emerges as the winner for now, while biochemistry has remained a niche alternative. The government will have to set the standard, Hertzberger concludes, because industry on its own is not going to solve the major societal challenges internally.
That does not detract from the fact that hard work is being done on this every day, as shown by four WUR 'biobased research' programmes, which were reviewed during the symposium.
Safe and circular biobased products
Jacco van Haveren (WUR), manager of the Safe and Circular Biobased Products Programme, bit the bullet. This programme is about replacing fossil-based resources with renewable, biobased alternatives that are 'by design' safe and circular at the same time. Consider pigments, coatings and composites, along with agents that end up in the sewage after use, for example detergents and personal care products. “We are developing technologies with industry to make all the components of these complex formulations – including surfactants, thickeners, plasticisers, complexants and solvents – biobased and biodegradable, with toxicity screening in place at an early stage, supplemented by predictive tools for functionality."
We would like to go for 100% circularity, but we are part of the chain and cannot exert influence on all the links.
André van Linden of Akzo Nobel Paints & Coatings, one of the industrial partners in this programme, said: "We would like to go for 100% circularity, but we are part of the chain and cannot exert influence on all the links." For example, only 2% of Akzo's ecological footprint is determined by its own operations. Suppliers (46%) and customers (30%) have the largest impact. End-of-life options are also limited in the case of paints and coatings, as they are applied as thin layers onto other products and cannot be separated from them again. While adjusting the formulation and replacing fossil-based raw materials with renewable ones (such as bio-aromatics) are certainly options, they are still in their infancy and will have to be done gradually.
Designer polymers from microbes
One approach currently in the spotlight is the production of natural (bio)polymers by means of microorganisms. Researcher Frits de Wolf (WUR) is an expert in this field and presented full-mcl-PHA and protein polymers. The latter have been around for thousands of years: consider the production of natural silk, collagen, leather, gelatine and casein. The execptional properties of these protein polymers
are an inspiration for the development of new protein polymers with specific
properties. Wageningen Food & Biobased Research is currently creating designer polymers from yeasts and bacterial cells.
"We design and construct synthetic genes that we introduce into yeast cells, which will produce and secrete the polymers for us according to the instructions of the genetic code," De Wolf explains. “Each molecule here is an exact copy of another." The polymer can be isolated, and purities of 99% can be achieved. This brings within reach applications in areas such as foodstuffs, personal care products, and also pharmaceutical applications such as drugs and scaffolds (auxiliary structures) that dissolve in the body.
Renewable synthetics
Synthetics are everywhere and will remain so for the time being, Karin Molenveld (WUR), manager of the Renewable Plastics Programme, believes. But this poses two problems: the use of fossil resources responsible for climate change and the accumulation of microplastics in the environment. “This is the reason we are developing circular plastics from biobased raw materials, and so starting the design process at the end." This means that the focus is not on performance, but on the demand for circularity. New plastics are being developed, processed and tested that can be industrially produced but do not accumulate in the environment.
For example, the 'bio-polyesters of the future' that Patrick Farquet, head of Renewables & Biobased Applications at Sulzer Chemtech, talked to us about. This includes the use of lactic acid. Lactate is purified and converted into lactide (cyclic dimer of lactic acid) which forms the basis for the production of PLA (polylactic acid). Sulzer has developed a continuous process for ring-opening polymerisation processes to manufacture biodegradable plastics from cyclic dimers. Apart from PLA, this process is suitable for producing PCL (polycaprolactone), PGA (polyglycolic acid) and various co-polyesters. Sulzer has now applied the technology on a pilot scale and can provide samples for application development. The company is looking for partners to explore new opportunities.
I expect the market for starch-based biopolymers to grow strongly in the years ahead.
New plastics are also being made from starch – the area of expertise of researcher Fresia Alvarado Chacon (WUR). "I expect the market for starch-based biopolymers to grow strongly in the years ahead," she says. “Starch is, after all, a renewable resource that is abundantly available and biodegradable in all environments, as well as being soluble in water." There has for this reason been plenty of work on characterising starch-based plastics, developing models to predict the properties of the final product and on processing these polymers through extrusion and in an injection moulding machine. Foams have also been made for egg cartons, for example, which weigh less than paper cartons and so have a lower ecological footprint.
Natural materials
Utilising the functionalities nature has to offer and adapting them to the applications of everyday life – this is the core of the work in the Nature-Based Materials Programme. "We are frequently asked the question: 'I have this kind of biomass, what can I do with it?' Of course we can turn it into packaging and we already do. But even more important is to develop its full potential as part of sustainable value chains," programme manager Edwin Hamoen (WUR) says. Applications can, for example, be considered for specific components of biomass in addition to packaging, such as building materials, textiles and ingredients. This is definitely not just about technology, but about utilising the entire chain, from the production or collection of bio-resources from agriculture, forestry and nature management through processing or 'pretreatment' for industry and manufacturing to the take-up and further application of the end products. It requires the involvement of local parties from all along the chain.
We are frequently asked the question: 'I have this kind of biomass, what can I do with it?'
A good example is biobased construction, where locally grown raw materials, such as wood, Miscanthus and hemp, can be used. The national Building Balance Programme focuses on initiating, promoting and supporting independent regional and national production chains for biobased building materials made from these raw materials. Seven regional projects are now running in the Netherlands.
Arne Eindhoven of the Raw Materials Collective (Grondstoffen Collectief) addressed the Circular Biobased Products Symposium on his involvement in this in Gelderland. The province has outlined the aim there of making the construction of 30% of all new houses biobased. Housing associations are collaborating, and dozens of Gelderland farmers have now started growing hemp and Miscanthus to produce construction panels and insulation materials from natural fibres. They will receive carbon credits as an additional (future) source of income. This will soon require larger factories, demanding tens of millions in investment. And a plan is being drawn up with other regions for a joint fibre refinery. Setting up fibre cooperatives to give building contractors a central point of contact is also being looked into. Attention is also being given to various issues around this, such as certification, mortgages and permits.
Binderless construction boards
Wageningen Food & Biobased Research is in the meantime also working on the development of new biobased building materials, such as binderless construction boards. These are panels made by compressing and heating lignocellulosic biomass. Adding binders such as glue or resin is unnecessary here. Gijs van Erven (WUR) related how the initiative arose years ago owing to a need to process coconut shells. "We now also understand how the mechanism works at the molecular level and have further developed the technology so that we can better control the process." It now also works with Dutch local residue and side streams. This facilitates the manufacture of 100% circular biobased board material in various qualities, similar to MDF or Trespa. Industrial partners are still being sought for the new 'More with Binderless' project to take the process further.
Circular water technology
Water is a key element when working with natural resources and essential for humans, animals, nature, food production and a host of industrial processes. It seems abundant on Earth, but that is a misconception. "Only 1% of all water on earth is available as fresh water," says Irma Steemers-Rijkse, manager of the Circular Water Technologies program. "So who gets the water when there are shortages becomes an important question. Is it for agriculture, industry, consumers?"
So who gets the water when there are shortages becomes an important question. Is it for agriculture, industry, consumers?
At the same time, numerous substances end up in water. Human activity and water use put all kinds of harmful substances, such as drug residues and detergents into the water environment . And industry spends a sloppy $44 billion a year (2020 figure) on chemicals for water treatment, against limescale, rust, microorganisms, or for flocculation in water treatment. Most of these agents are fossil-based and non-degradable. The challenge is therefore to find alternatives that are safe, biodegradable, renewable and preferably made from side- or waste streams.
Rainer Haug of Kurita, who specializes in systems and chemicals for water treatment in industry, emphasizes that they are necessary for protecting watersystems, for example, a cooling tower. In it, water circulates and is repeatedly heated and cooled, continuously evaporating water and thereby increasing the concentration of dissolved substances. Biobased chemicals are not necessarily more environmentally friendly than fossil ones, according to Haug. "They can still be aquatoxic. There is no easy solution to that.". However, the need for a sustainable transition is recognized and also being worked on by Kurita.
Ben van den Broek of Wageningen Food & Biobased Research is researching biobased (polysaccharide-based) anti-scaling agents for cooling water systems. Limescale inhibition is now done with phosphates or polysulfonic/carboxylic acids, but the former cause unwanted algae growth and by-products upon discharge and the latter are by definition not biodegradable. Modified starch and inulin are possible substitutes but, with extensive modification, are less biodegradable. Chitosan and alginates are both well biodegradable and can bind limescale without modification. Using chitosan and alginate together provides synergy benefits.
New projects 2024
In 2024, a number of new project ideas will be launched in which Wageningen Food & Biobased Research is working along with industry, research institutes, NGOs and other interested parties. For instance, 17 new projects are now planned in the four programme areas. Public-private consortia are being set up for this purpose. The project ideas can still be adapted to the research needs of partners wishing to join these consortia.
Check here for an overview of new project ideas and options for joining as a partner: