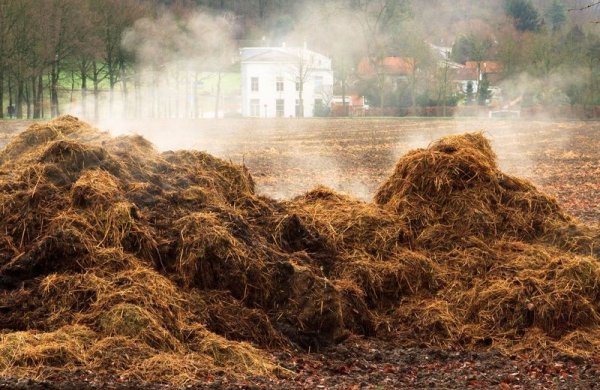
Longread
How to turn manure into valuable products
Manure is no longer seen as a waste stream, but as a valuable raw material. More and more technologies are being developed to convert manure into valuable organic and inorganic nutrients for agriculture. This is helping to close agricultural nutrient cycles at the regional level, ensures optimal use of the available nutrients and minimises harmful losses into the environment. Oscar Schoumans, a researcher at Wageningen University & Research, is an expert in this field.
Animal manure contains lots of nutrients such as phosphate and nitrogen that play an important role in soil fertility and plant growth. However, the large numbers of animals kept in the Netherlands on a relatively small area has led to a mineral surplus: more phosphate and nitrogen are produced than can be introduced to the soil without polluting ground and surface water. Moreover, the sector produces too much ammonia and greenhouse gases which are released to the air.
One way to do this is to replace artificial fertilizers with alternative products. According to fertilizer and environment expert Oscar Schoumans of Wageningen University & Research, these surplus nutrients must be recovered from animal manure to close the nutrient cycle. The manure/phosphate surplus will need to be removed from the Dutch agricultural nutrient cycle and used elsewhere.
Circular agriculture systems focus on processing residual biomass flows into products that can be used in the region.
Currently, the urine and faeces from indoor livestock are usually combined as slurry and used on the farmer’s own land. When there is a surplus of this slurry, it is exported directly abroad or sold to a manure processor who separates it into a liquid and a solid fraction. “The thick, phosphate-rich, organic manure is often exported to neighbouring countries, sometimes after first drying and processing it into granules,” Schoumans says. “This means a percentage of the organic matter and nitrogen is also lost abroad. In addition, the transport of these bulky products costs a lot of energy, produces high CO₂ emissions and is expensive for farmers and manure processors.”

Circular agriculture focuses on the recovery of the nutrients from manure and the production of fertilizer products that can be used in the region without harming the environment. For example, the surplus phosphate can be removed and sold separately as a raw material to the fertilizer industry, while the nitrogen can also be extracted and converted into a fertilizer substitute that can be applied on top of the quota allowed by the nitrogen application standard for animal manure. “Improvements in a number of technologies in recent decades are making this easier to achieve.”
Nutrient recovery
Schoumans and his colleagues at Wageningen University & Research aim to develop products that are suitable for fertilizing farm crops and can replace artificial fertilizers where possible. “Ten pilot projects in the field of nitrogen and potassium recovery from the liquid fraction of pig manure have already made much progress. With the help of membrane technology (reverse osmosis), clean water is separated from the manure and can be safely discharged, leaving us with a mineral concentrate rich in nitrogen and potassium.”
According to Schoumans, processing the liquid fraction more or less doubles the concentration of minerals. The next step is to ease the restrictive legislation and regulations. “The European Union has permitted these pilot projects to use the mineral concentrate as a nitrogen fertilizer substitute, but this is still not allowed under the European Nitrates Directive. This directive stipulates that all nitrogen products from animal manure must be treated as nitrogen in the form of manure.”
Mineral concentrates extracted from animal manure can be converted into fertilizer products to replace nitrogen fertilizer.
There are various European initiatives to change these criteria for nitrogen products from animal manure, Schoumans notes. “If the proposed RENURE criteria (REcovered Nitrogen from manURE) are adopted by the European Commission, these products will probably be approved as fertilizers in the future.” This will lead to a fully-fledged replacement for artificial fertilizers.
Another method is nitrogen stripping. The temperature and/or the pH value of the liquid fraction is increased, producing an ammonia-rich vapour that is passed through an acidic solution and so fixes the ammonia as ammonium again. More recently, membranes have been used that only allow gases to pass through, but these only work if almost all particles from the liquid fraction have first been captured.
Both methods for stripping ammonium from the liquid fraction result in a pure ammonium solution such as ammonium sulphate or ammonium nitrate. For farmers, these products are just as good as the ammonium sulphate and ammonium nitrate produced by the fertilizer industry. The purer these nitrogen products are, the better their nutritional value can be calculated and the more opportunities will be revealed for using them as fertilizer substitutes.
Nitrogen emissions
In addition to their nutritional value, to protect our drinking water it is important to prevent nitrates leaching from the soil into the groundwater. “We have found slightly less nitrates leach from mineral concentrates than from slurry and artificial fertilizers.”
The researchers also measured emissions of ammonia and nitrous oxide (laughing gas) into the air from mineral concentrate. Emissions were high when the concentrate was sprayed just above the surface, but when it was introduced into the soil, for example with agricultural machines that lay narrow strips of the concentrate on the ground, a large part of the ammonia and nitrous dioxide emissions to the air can be prevented. “If these products are applied in a way that reduces these emissions, they can compete with artificial fertilizers in terms of their environmental footprint,” says Schoumans.
Phosphate removal
In addition to processing the liquid fraction of animal manure, technologies are also being developed to remove phosphate from the solid fraction. The company Groot-Zevert Vergisting of Beltrum, in the Achterhoek region, cooperated with Wageningen University & Research and the business community in the development of the Groene Mineralen Centrale (Green Mineral Plant). This installation not only produces mineral concentrate from the liquid fraction, but also extracts phosphate from the solid fraction using a new technology. “The organic matter that remains is low in phosphate and sold as a product called ‘Green Effective Soil Improver’. The mineral concentrate is used to produce ‘Green Field Manure’ by mixing it with other nitrogen products, some of which are recovered from other flows,” says Schoumans.
A by-product of the recovery of phosphate from animal manure is organic matter that can be used as an effective natural soil improver.
Green Field Manure is being applied at the regional level in a pilot collaboration called ‘Fertilizer-free Achterhoek’ that was launched in 2018 and involves LTO Noord (a farmers’ organization), Wageningen University & Research and other stakeholders. The phosphate surplus that is extracted from animal manure as a phosphate mineral is used by the fertilizer industry or regions with a phosphate deficit.
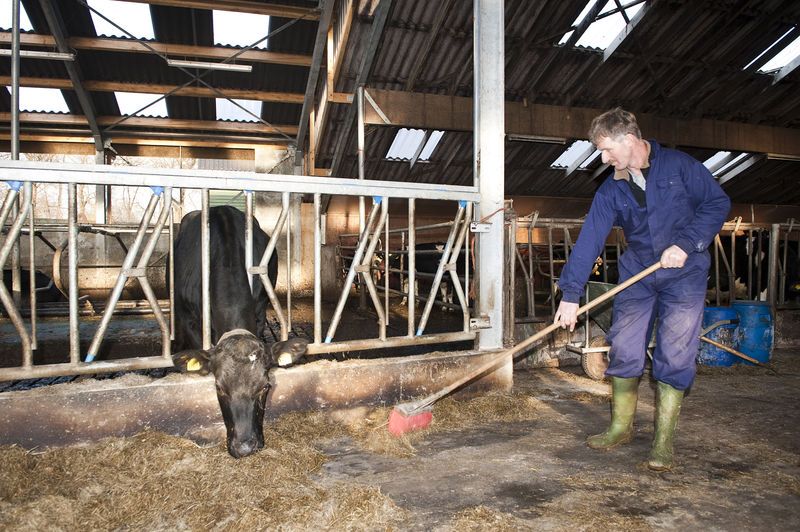
“This alternative for nitrogen fertilization replaces the artificial fertilizers used in the region and at the same time retains the organic matter and minerals in the manure to the benefit of soil quality,” explains Schoumans. “The result is a nutrient cycle that is as closed as possible.” The fermentation process at the Green Mineral Power Plant produces energy in the form of biogas, electricity and heat. The Green Mineral Plant is being evaluated as part of the Horizon2020 programme, a major European research project.
Fermenting animal manure yields energy in the form of biogas, electricity and heat
In the Ecoson pilot project in Son, in Noord-Brabant, pig manure from some 70 pig farms is used to produce biophosphate granules for export to farming regions in Europe with a phosphate deficit. In addition, the project produces 2,500,000 m3 of green gas annually which is supplied to the gas distribution network in the Eindhoven region. This is enough for the annual consumption of 1,700 households and results in a CO₂ reduction of approximately 4,500 tonnes per year.
Poultry manure is also suitable for generating green energy through incineration, says Schoumans. This is currently being done by the company BMC in Moerdijk, also in Noord-Brabant, where the manure of four hundred Dutch poultry farmers is processed. The organic fraction of the poultry manure is fully combusted and the flue gases are purified. Unfortunately, the nitrogen produced is released back into the air, remarks Schoumans. After incineration, a small volume of ash remains that is rich in the nutrients potassium and phosphorus and is suitable for export as fertilizer or for further processing in combination with other products.